Elevate Your Products with R-PVB Leather Component
Unpack R-PVB Leather Component
Recycled PVB leathers are sophisticatedly engineered materials composed of three distinct layers, each contributing unique attributes to the overall quality and aesthetics of the product. These layers are: Surface Finish, Recycled PVB Film, and Base Fabric. These layers function both individually and synergistically, ensuring the recycled PVB leathers not only perform effectively but also maintain a superior aesthetic appeal.
01
Surface treatment
The outermost layer embellishes the product with a myriad of external features. It offers a diverse spectrum of colors, intricate textures, and captivating patterns, enhancing the visual appeal and tactile experience.
02
Recycled PVB film
Recycled PVB films is situated in the middle and seamlessly bonds the base fabric with the surface finishes. Beyond its adhesive properties, it modulates the material’s tactile flexibility and augments its physical characteristics, ensuring the composite material meets its inherent quality specifications.
03
Base fabric
Positioned at the bottom, this foundational layer bestows the leather with its primary physical attributes, including tensile strength, tearing resistance, and sewing durability.
About PVB
What is PVB?
Polyvinyl butyral (PVB) is a material specifically engineered for use in safety glass. This type of glass, when laminated with a PVB film under conditions of high heat and pressure, becomes resistant to blasts, heat, and ultraviolet radiation, while also offering acoustic insulation. Such safety glass finds widespread applications in various fields, including vehicles, furniture, and construction, with its most notable use being in windshields.
Why do we use recycled PVB (R-PVB)?
PVB possesses special adhesiveness, flexibility and toughness, and excellent weather resistance. It is also a more eco-friendly substitute to other plastic material such as PVC, PU, etc.
Its primary industrial use is as an interlayer film in safety glass, which is used in automobile windshields, architectural glass, and solar panels.
The purification process of recycling waste PVB includes separation, purification, and modification. The recycled PVB, through the purification process, can have the following characteristics according to product needs:
– Compliant with the European Union’s REACH environmental regulations.
– Reduction in carbon and water emissions.
– Free from dioxin pollution.
– Excellent weather resistance, non-hydrolyzing, suitable for outdoor products.
– Does not contain DMF (Dimethylformamide).
– Customizable physical properties to meet design and functional requirements.
How is PVB recycled?
Recycling PVB is a multi-step process, largely due to the need to separate the PVB from other materials it is typically combined with, such as glass in laminated safety glass. Here’s a general overview of the recycling process:
Collection and Sorting: The first step is collecting and sorting the PVB-containing materials. For instance, in the case of windshields and safety glass, these need to be gathered and sorted separately from other types of glass and waste.
Size Reduction: The collected material is then typically broken down into smaller pieces. This can involve crushing or shredding the glass-PVB laminate to make the subsequent steps more efficient.
Separation of PVB from Glass and Other Materials: Using mechanical separation and chemical and solvent treatment to separate PVB from impurities.
Purification of PVB: After separation, the PVB may undergo further purification to remove any remaining impurities, such as small glass particles or adhesives.
Processing and Modification: The purified PVB can then be processed for reuse. This may involve melting and reforming it into sheets or incorporating additives to modify its properties for specific applications.
Reuse in New Products: Recycled PVB can be used in various applications, such as new safety glass production, new plastic products, or even artificial leather (our star product).
Applications
Our R-PVB leather component is adaptable for various uses, come with diverse surface finishes and customizable physical characteristics. Perfect for industries in shoes, furniture, handbags, sporting balls, apparel, automotive interior decorations, and many more. Contact us for more information.
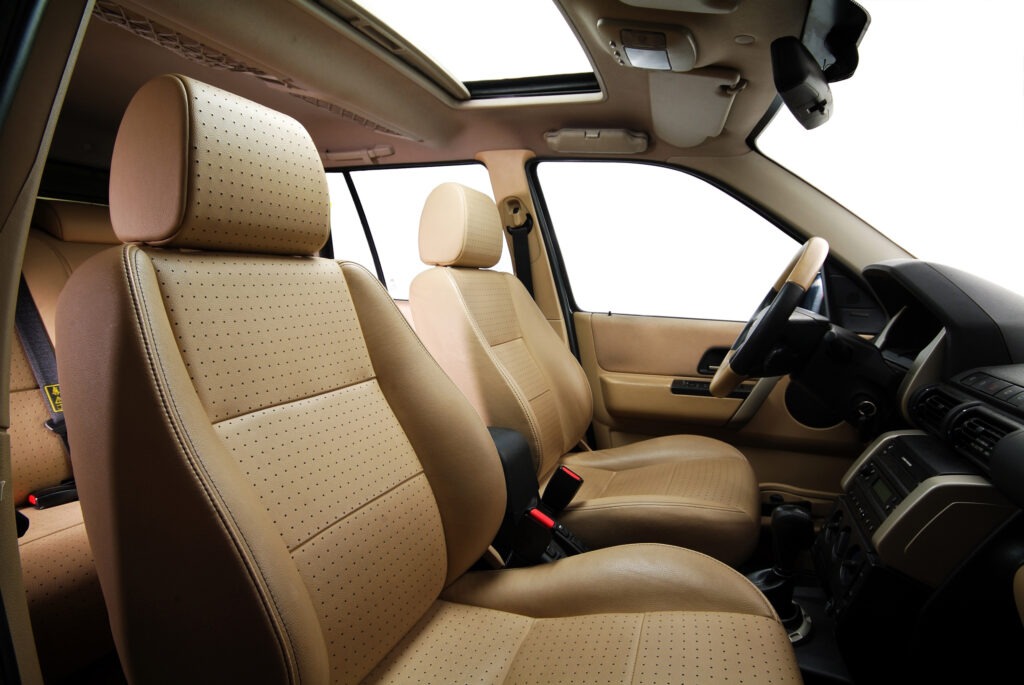
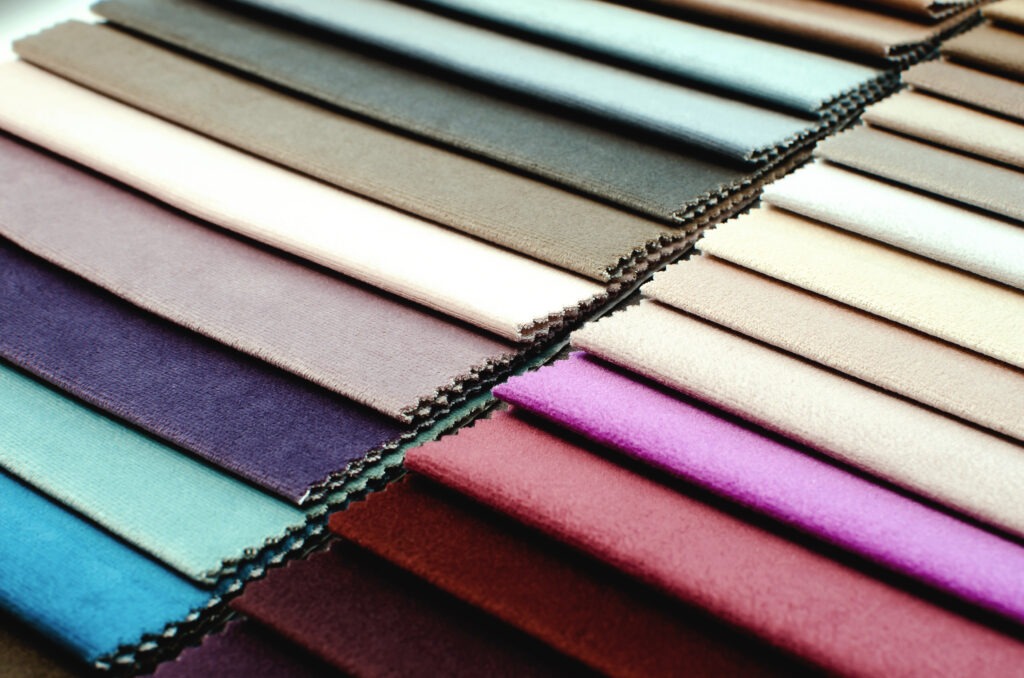
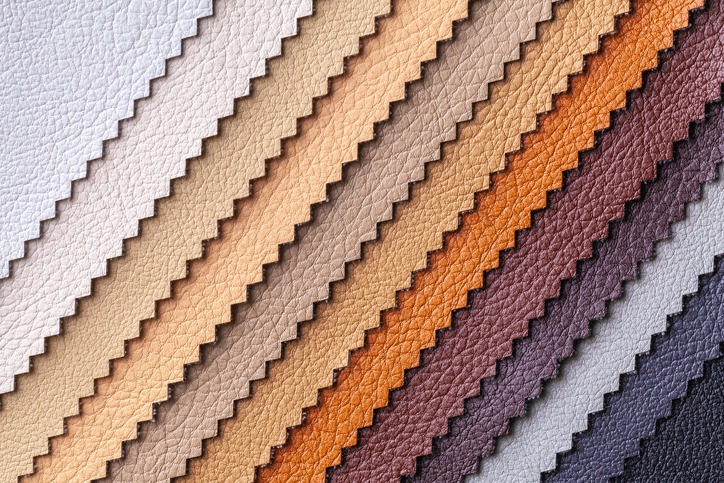
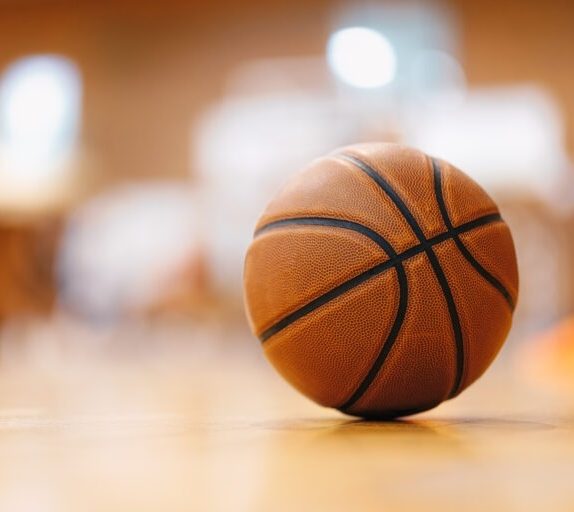
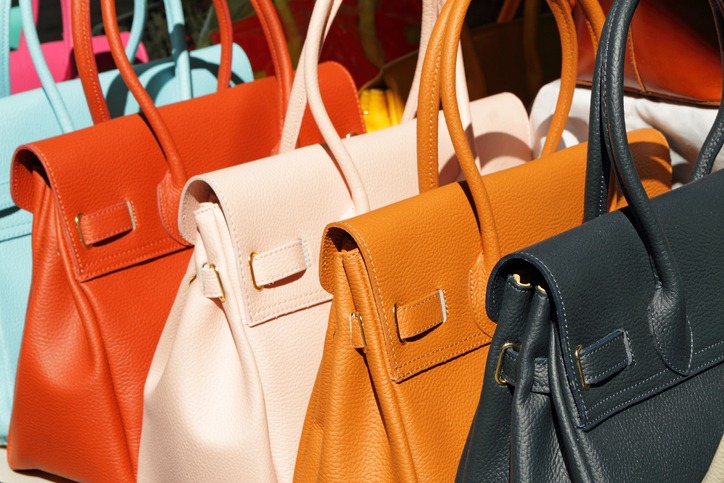
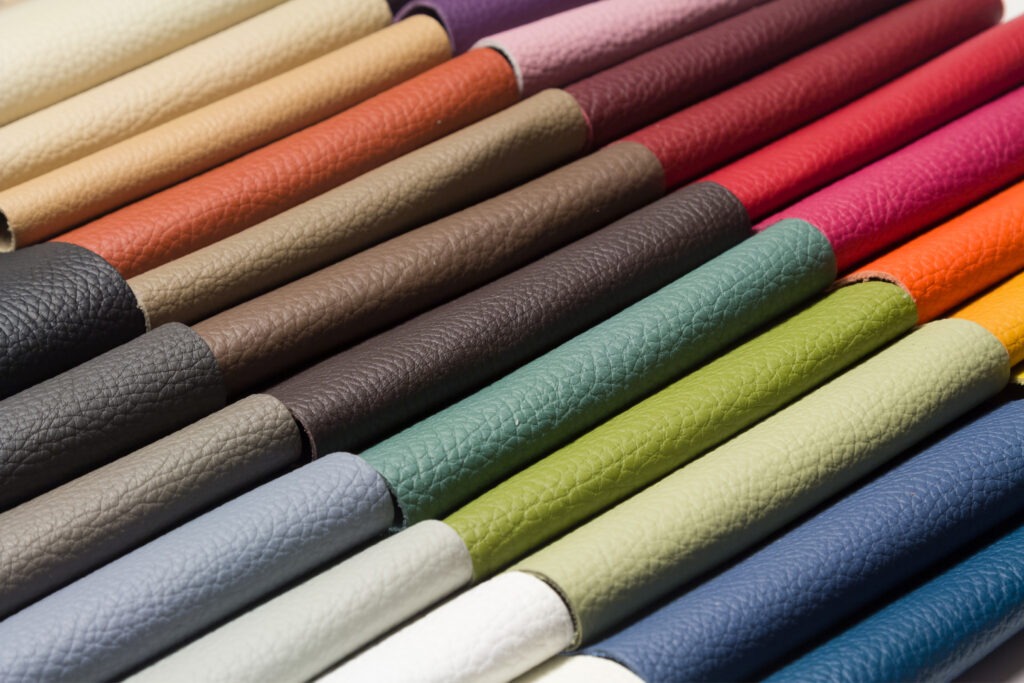
Properties and Comparison
R-PVB leather component properties
No | Item | Standard Value | Maximum Value | |
---|---|---|---|---|
01 | Bonding Strength (kg/cm) | 0.6 | 2.5 | |
02 | Flexility (cycle): 25°C | 80,000 | 200,000 | |
03 | Flexility (cycle): 0 °C | 80,000 | 30,000 | |
04 | Abrasion (ASTM D-3884) | 1,000 | 5,000 | |
05 | Tensile Strength (kgf/cm) | 20 | 90 | |
06 | Tearing Strength (kgf) | 20 | 75 | |
07 | Fogging | 70.0% | 94.2% | |
08 | Feel to Hand | 18 ~ 85 ShoreA | ||
09 | Weather Resistance | Anti-hydrolysis | ||
10 | Environmental Protection | REACH, GRS, Low Carbon Emissions |
Comparison of artificial leather material
No. | Item | R-PVB | PVC | Watert-based PU |
---|---|---|---|---|
01 | Chemical Name | R-Polyvinyl Butyral | Polyvinyl Chloride | WB Polyurethane |
02 | Carbon emission | Low | High | High |
03 | Weather resistance | Excellence | Excellence | Hydrolysis |
04 | UV resistance | Excellence | Excellence | Poor |
05 | Dioxin pollution | Nil | Pollution source | Nil |
06 | Regulatory compliance | REACH | REACH | REACH |
07 | Recyclibility | Recyclable | Recyclable | Non-recyclable |
08 | Genuine leather similarity | Identical | Platic-like | Similar |